The most common type used at WVNS and in industry is 6 x 19. This is six strands. Sling Eye Design the Did Ratio is expresse Sling eyes are designed to provide what amount to 'small inverted slings' at the ends. Hoisting & Rigging Fundamentals.
The engineering tool is validated by comparing the load capacity results with Roark and the FEA results for padeye geometries used in projects performed by Seaway Heavy Lifting. From this comparison it is concluded that the derived tool gives an accurate load capacity for padeye geometries within a specific range. Welcome to the the spreadsheet for Pad-eye design! - SI Units What does this Excel Sheet do? This Excel sheet helps you design a pad-eye to be used for lifting or lashing during transport It can be used for the design of a standard pad-eye with 1. No brackets 2. Single cheek plate on either side It makes the following checks 1. From design stand point, per API RP 2A-WSD section 2.4.2.a, I have to design the pad eyes for 5% of the static sling load as a horizontal out of plane load applied at the center of the pinhole. Theoretically this 5% will take care of almost 2degree and 52 second rotation of the pad eye out of that ideal plane.
- Forum Actions
- Quick Links
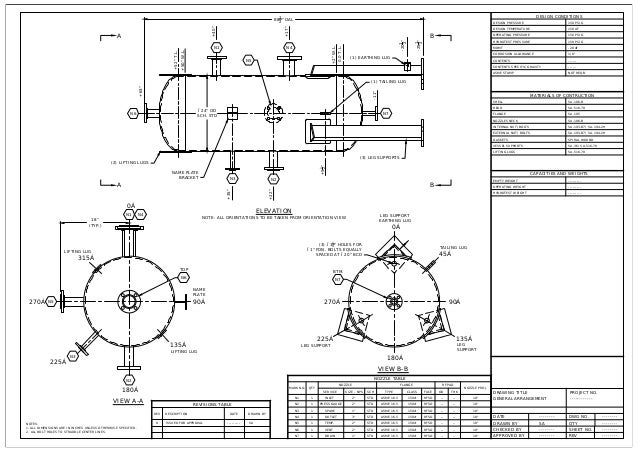
Thread Tools
Display
- Hot Rolled
- Join Date
- Apr 2010
- Location
- Apex, North Carolina - USA
- Posts
- 699
- Post Thanks / Like
- Likes (Given)
- 45
- Likes (Received)
- 62
This thread could turn into - 'Here's what happened when things went wrong...'
My father had an accident early on in his machine shop days (60's). He had a lathe fall on him. It was a weekend and he was moving machines alone. (First big mistake) Fortunately it didn't break anything (in him). He was pinned for while until he he was able grab a stick to pull other tools to him so he could lever himself out from under the machine.
After that, he was 'Mr. Safety' - at least while moving machines. - Cast Iron
- Join Date
- Jan 2009
- Country
- UNITED STATES
- State/Province
- Texas
- Posts
- 453
- Post Thanks / Like
- Likes (Given)
- 166
- Likes (Received)
- 127
Homemade machine dolly
After using for years the various ‘Egyptian’ methods of moving machines around, and after a small mill spun around 90 degree in a lift using a engine crane (cherry picker), and generally working alone…..I decided for safety sake (esp with very top heavy machines) that I needed to make a dolly of some sort to move machines around. It’s made from parts I had on hand (4 inch C-channel and HF casters for 3$ each half price sale). It works really well and now I realize I should have made this long ago. If I did again (and think I will) I’ll use heavier swivel casters and will weld small sections of pipe to the wheel supports so that I can turn the wheels by hand using a bar slid into welded pipe (the swivels do not swivel so easy with a ton of machine on them). This nice thing about this dolly is it lifts the machine for you – you have to get the hex bolts through the base which isn’t hard at all – an inch or two lift per side – once you’ve got bolts through base then add a nut to stop them from falling back through machine base and leave them there permanently. I have several old machines and they all have holes at each corner of their (bell shaped) cast base for bolting machine to the floor - this works for all of those machines. This dolly was made to just clear a 32 inch wide door. Other bolt patterns for other machines I have are easy to accommodate with another flat bar or channel section laid across top of dolly and appropriately drilled holes. The rails I extended intentionally a little past the wheels to get an automotive floor jack under them as I have small ‘steps’ in my floor slab I have to get over. The dolly is sturdy enough to jack up one corner and the other corner lifts too with a 2000lb mill on it - and so then I can pull floor jack with dolly and machine over small ‘steps’ of several inches in my slab. The bolts are (hex head down) placed through the base of machine and then through dolly are evenly tightened to lift machine a quarter inch to several inches off the floor – very safe even if a wheel were to collapse. The pictures are showing machine on pipe rollers and lumber which is not a pertinent to the dolly at all – just how I stored the machine before creating dolly
- Hot Rolled
- Join Date
- Jan 2008
- Location
- Blythewood, S.C.
- Posts
- 625
- Post Thanks / Like
- Likes (Given)
- 0
- Likes (Received)
- 40
Homemade machine dolly
Kgize;
What an exceptional clever idea for a dolly that you have made.
I just purchased a Millrite milling machine and I have been thinking about how I am going to roll it through the door of my basement shop from out on the lawn of the back yard.
With your permission I will build such a dolly.
Best Regards;
Steve - Plastic
- Join Date
- Feb 2008
- Location
- New York
- Posts
- 20
- Post Thanks / Like
- Likes (Given)
- 0
- Likes (Received)
- 0
For a drill press I used one of thoes heavy duty dock workers hand truck,metal bottom with heavy wood frame and solid rubber tires.Put the base on the bottom slide the table down onto the top cross piece of the hand truck and tie that to the hand truck with a load binder.Never had a problem.Lathes,bridgports,big band saws and surface grinders a johnson bar and 1.'dia round stock and a wrecking bar to move it,while another person keeps on moving the 1' bars,We never had one fall that way.Need at least two people for safety sake.
- Cast Iron
- Join Date
- Jan 2009
- Country
- UNITED STATES
- State/Province
- Texas
- Posts
- 453
- Post Thanks / Like
- Likes (Given)
- 166
- Likes (Received)
- 127
Steve – I spent the time to post just for such a purpose – I’d be honored to have the idea copied - PM me a picture when done..
Some tips: - make sure your casters are tall enough to leave room to lift the machine taking into account the height of machine’s base where the floor mounting holes are. I used casters with ‘tires’ (claimed ‘cast iron and molded rubber’) that are a little soft once you really put some weight on them, and they slightly flatten if machine left on them for long time – get very hard compound for the ‘tire’ on the caster wheels or all steel. Do yourself a favor and make all 4 corners swivel wheels. The extension of rails for floor jacking was a better Idea than I had thought – I would make the extensions (sticking out from casters) longer than I did to make floor jacking more secure and for putting blocks under them – with blocks under the rails extensions – and blocks under the machine for leveling and/or raising the machine – raising dolly then machine and back again - this dolly could in theory lift the machine - by tediously cranking the jacking nuts up and down and placing the appropriate blocks - straight up through the ceiling onto another floor… - Diamond
- Join Date
- Feb 2004
- Location
- peekskill, NY
- Posts
- 24,146
- Post Thanks / Like
- Likes (Given)
- 0
- Likes (Received)
- 4382
HOnestly I'm suprised nobody's mentioned this technique here yet.
I use a mulligan to help move heavy items in the shop!
http://www.metalworking.com/RCM-gall...m/Mulligan.jpg
many hands make the lights work.... - Hot Rolled
- Join Date
- Apr 2007
- Location
- Central MA
- Posts
- 984
- Post Thanks / Like
- Likes (Given)
- 0
- Likes (Received)
- 23
Why, using a pallet jack, of course! About 4k pounds of horizontal mill:
- Aluminum
- Join Date
- Jan 2012
- Country
- UNITED STATES
- State/Province
- Oregon
- Posts
- 117
- Post Thanks / Like
- Likes (Given)
- 7
- Likes (Received)
- 43
I've been searching Google for a week looking for the best way to move my BP, and your solution looks great.... when done moving, simply dismantle it and store it for future moves. I'm gonna be working on mine soon. Thanks.... Dan
- Diamond
- Join Date
- Apr 2004
- Location
- Shandaken, NY, USA
- Posts
- 4,225
- Post Thanks / Like
- Likes (Given)
- 1104
- Likes (Received)
- 6640
For lifting and assembling machine tools in my basement shop, I hang a chainfall from the overhead. To do this, I first locate machine tool at a good location for a pick point in the overhead. I lag a 2 x 8 or 2 x 10 to the first floor joists, locating it very close to one of the carrying girders. This minimizes any bending moment and gives negligible deflection in the joists. I then mount a forged steel weldless eye, or a lifting lug (a fabricated plate steel 'tee' with a hole for a shackle), or a forged steel 'eye nut' (whatever comes to hand from my bin of miscellaneous rigging stuff).
Once I have the picking point, I hang a chainfall or chain comealong and pick the machine tool parts to assemble them. For machine tools on the order of a Heavy 10' Southbend lathe, a Burke Milling Machine, or putting a 12' Troyke rotary table on my Bridgeport, this system of rigging works well.
To move machine tool parts around the basement shop floor, I use either a furniture dolly or a hand truck. I use ratchet strap binders to secure the machine tool parts to the dolly or hand truck to be sure they cannot turn or tip off.
To get machinery in and out of the basement, I have several methods. One is to put a couple of planks on the basement access stair to create a ramp. When I put my Heavy 10' Southbend Lathe into our basement, I had it on wood skids. We moved it around the outside of the house by putting the lathe on a furniture dolly and binding it to the dolly. We put down plywood, and leapfrogging the plywood for a runway. The lathe rolled easily enough on the furniture dolly ( an ancient hardwood thing that probably moved pianos in its day). When we got to the basement entry, we got the lathe raised on blocking using a pinch bar. We had it off the dolly, so it was sitting on its skids. Once it was high enough to clear the lip of the basement entry (Bilco doors), we used a chain comealong tied off to a shackle in the step bumper of my old Cornbinder Scout to let the lathe down.
We soaped the ramp planks on the steps with Ivory Soap, and the lathe slid down them. Once in the basement, I pinched it up using a 30' 'sleever bar' and blocking. Got it back on the dolly and where it needed to go. Used the pinch bar and blocking to get the lathe off the dolly and then off the skids. I made the move in the basement working alone.
round column drill presses are fairly light and easy to move. My method is to use the quill as a jack to raise or lower the head on the column. I put a piece of plywood on the table and run the chuck jaws so they are fully opened (unless the chuck/arbor can be removed from the spindle). I bought a Powermatic Drill press down in NYC and I was wearing a white shirt, tie, and good pants. I had a Ford Bronco at the time (1983). The seller had the drill press disassembled for me, so it went into the Bronco in pieces easily enough. I drove upstate, and offloaded it by myself. As I recall, I slid the head out of the Bronco, and down a plank. I got it onto a hand truck and down the stairs into the basement. I took the base/column down on the hand truck, and carried the table. I got the table onto the column, and laid the column/base on its side. I used some blocking for the head, and was able to get the head onto the column with the drill press laying on its side. I slid the head down the column so it was near the bottom, spindle touching the table, table locked to the column. I locked the head to the column so it could not turn. The column gave me enough leverage to easily 'walk it up'. Once the drill press was stood up, I used the quill to jack the head up the column. I was still in my white shirt and tie, excited at bringing home the drill press and not bothering to change clothes as it did not seem to be much of a job. I stayed clean, and I think the whole business of moving the drill press from the Bronco and setting it up consumed all of 30 minutes.
A drill press is top-heavy, so if you try to slide it, be careful as it can tip. If you mount it on a wider base, it can be slid with less chance of it tipping. - Hot Rolled
- Join Date
- Apr 2010
- Location
- IN, USA
- Posts
- 536
- Post Thanks / Like
- Likes (Given)
- 9
- Likes (Received)
- 173
Drive it.....Originally Posted by wb2vsjOT: How do you move heavy equipment around your shop? - Cast Iron
- Join Date
- Mar 2007
- Location
- Westford, Massachusetts
- Posts
- 409
- Post Thanks / Like
- Likes (Given)
- 22
- Likes (Received)
- 4
This is my preferred method - I've got a smooth, flat concrete floor. I use four+ pipes, and depending on the footprint and weight of machine one or two thickness of 3/4' plywood. If heavy enough, might need hardwood beams too. I use 3/4'black iron pipe 'cause I have a bunch of it in various lengths for pipe clamps. Keep at least three pipes under the load, and you can turn the load by angling the pipes in the direction you want to turn. You need at least another pair of hands to move the pipe after if clears behind the machine while you hold machine in place. I've not had trouble getting up to ~800 lbs moving and controlled in this way.Originally Posted by bigearl67I have been doing this a lot lately with building the new shop. Typically I use 1 inch round stock as rollers with a come-a-long pulling. Chains, straps and have even used my Jeep quite a bit when possible. When I poured the concrete slab I stuck a nice big eye bolt in the far corner and have a heavy strap secured to it. That was one of my better ideas and has been a blessing.
Be careful, as the rolling pipes are a scary pinch hazard. I'd roll them well clear with the sole of my boot before trying to pick them up and move to the front... same thing - put down well clear of the direction it's moving and roll into place with bottom of boot. - Plastic
- Join Date
- Apr 2012
- Country
- UNITED STATES
- State/Province
- New York
- Posts
- 13
- Post Thanks / Like
- Likes (Given)
- 11
- Likes (Received)
- 1
Knuckleboom on amphibious HMLC (Alvis Stalwart FV624) - Diamond
- Join Date
- Apr 2004
- Location
- Shandaken, NY, USA
- Posts
- 4,225
- Post Thanks / Like
- Likes (Given)
- 1104
- Likes (Received)
- 6640
Pulling on anchors set in concrete can be bad business. At our powerplant, a contractor was attempting to move a heavy transformer (about 180 tons). It sat on rail wheels on rails. It was a new transformer, and the manufacturer had failed to properly design the rail trucks (bogies in the UK) to equalize load. The result was the transformer wheels were not all bearing load and some of the wheel flanges were actually binding against the rails.
The contractor put a few wedge type drilled-in anchor bolts, on the order of 1/2' diameter, into the concrete deck slab, which is an extremely heavy mass of reinforced concrete. The crew then cut some 'lugs' out of scrap structural steel, in line with each rail. They hooked on some heavy comealongs and attempted to move the transformer. The transformer was bound on the rails. By way of comparison: we used to move the old transformers on the rails with nothing more than light comealongs or light truck winches. This new transformer was not going anywhere. Instead, one of the lugs pulled out of the concrete. It flew hard and fast and nailed one of the contractor's crew in the leg. He sustained a leg wound that required an ER visit and some time off work to recuperate.
The drilled-in anchors had held, but the concrete around them failed, shearing out in the classic conical pattern. Each drilled-in anchor had a neat cone of concrete with it.
As an engineer, I have a healthy respect for the forces developed in rigging. While the load applied to a pad eye, lug, or eyebolt may not seem like much, if applied in any direction by straight along the centerline of the anchor or eye, it will produce a bending moment. This can act like a 'pry bar', wanting to pull anchors out of the concrete with a much greater force than the load actually applied to the pad eye or lug. This is a case where leverage works against you rather than helping.
My own rules for designing these kinds of attachments to concrete are a bit more involved, but are also seat of the pants after 40 years of doing this kind of engineering. The first thing I do is to try to get some idea of what kind of concrete slab or structure I am going to be using to hold a lifting eye, dead man (point at which rigging or guy wires are tied off). If the concrete is punky, or the thickness of a slab is unknown, I will ask that it be at least drilled through to get an idea of thickness. I may sound the concrete with a mason's hammer. If the concrete looks like stuff that was batch mixed on site, is weathered and rebar is non existant, or a slab is thin (like 3 or 4'), it is a game changer. I may design pad eyes with multiple anchor bolts, spreading the load and going deeper with each bolt. I do a calculation of what the pull-out and shear loads on each anchor bolt will be. I then look up the manufacturer's published data for the type/size of anchor bolts I will be using. Unless I know what the strength of the concrete is, I assume fc' = 1500 psi. Normal design mixes for structural concrete have fc'= 3000 psi or 4000 psi.
If the concrete is good reinforced concrete, my other rule is to always use an anchor depth that gets the anchor 'inside' of the rebar. The first 2 or 3 inches of concrete is known as 'cover concrete' on reinforced concrete. It is generally considered as non-load bearing on things like slabs in bending or columns. My own rule is to count only the portion of an anchor that is 'inside the rebar' as carrying load. I do not like to rely on 'cover concrete'. the result is I design anchors so they are usually a minimum of 5' or 6' drill depth.
I rely on the anchor bolt manufacturer's published data for minimum spacing between anchors and from edges of slabs as well. I use a minimum factor of safety of 5 for anything anchored to concrete from which loads will be lifted or hung. If it is an anchorage for any sort of rigging, I use FS =5 , even if not used for lifting. If a lug or padeye plate has four anchors in it, I will usually assume only three are actually working to transfer the load into the concrete. The resulting factor of safety is then something like 6.6
Another thing I did was to get rid of any of the 'Red Head' or self-drilling anchors which use an expander cone. We do not use them for anything. These anchors are OK for shear loads. If they start to pull out, the expander cone does not cause them to wedge tighter. Once this type of anchor starts to pull out, it's gone.
I specify a type of bolt or expansion shield which uses a wedging action, the more the pull, the tighter it wedges in the hole. Most usually, though, I specify drilled-in anchor bolts set in resin grout. Or, I specify tapped steel sleeves, set in resin grout. The resin grout used for bonding anchors into concrete has some incredible strengths. When I design drilled in anchor bolts, depending on location, I will specify the grade of threaded rod. If it is a wet location, I may spec a high strength galvanized steel all thread (as spec'd by DOT for highway guide rail and bridge work), or else a stainless all thread with resulting reduction in strength. For any other uses, I spec B-7 grade all thread, a higher strength steel than normal 'hardware grade'.
The story of the moving of the transformer played itself out handily. After the accident, I was asked to take a look at things. Two things were immediately apparent. The transformer OEM had not machined real rail wheels. No angle on the tread, no angle or relief on the flanges. The treads and flanges were machined square to each other. The OEM had provided two-wheel trucks at each corner, but had mounted them 'stiff' to the bottom of the transformer. The bottom of the transformer was lighter steel plate with internal stiffeners and could be seen to have rippled from the welding. Daylight could be seen under at least one wheel.
I sketched up revised 'trucks' with an 'equalizer' or pivot to allow each truck's wheels to bear evenly on the rail. I also sketched up wheels with some draft on the treads and some relief angle on the flanges.
These changes were made to the trucks. I also designed a system of rigging to move the transformers. This relied on rail clamps as 'deadmen' instead of lugs anchored to the concrete. I calculated a worst case load based on locked wheels sliding on the smooth rails and called for the use of heavy chain comealongs with cable slings doubled through snatch blocks if need be. The rigging was designed with FS =5, and I also asked that dynamometers be placed between the comealongs and the deadmen. We had to move the transformer from where it was left when the lugs had pulled out of the concrete. I knew we had bound wheels, so asked that the rails and wheels be greased before we tried pulling. It took a heavy strain on the comealongs, nearly maxxing them out, and we needed the doubling up through the snatch blocks to get things to move. The transformer moved in a series of jerks or jumps, sliding on the greased rail with some of the wheels not rolling at all.
Once we got the rail trucks revised to my sketches, the transformer moved quite easily with no need of doubling up the rigging, no grease on the rails, all wheels carrying load and rolling instead of sliding or binding. Corporate acted like this was some big deal, but I told them otherwise. I reminded everyone that the design of wheels to roll on rails and the principals of using equalizers with multiple axles were well settled by the 1840's when railroads were coming into being. I had to give a presentation about the whole thing at a staff meeting, and said something like 'we had to reinvent the wheel for a vendor whom we paid to deliver a transformer on wheels that should have rolled in the first place'. I also stressed the fact that we had moved the deadman anchorage points from reliance on anchors in the concrete to solid connections on the steel rail. This also took the angularity out of the line of the pull and put it in a nice straight line.
Probably the funniest thing to come out of the whole thing happened when we were moving in the transformer with the revised wheels and trucks and the new rigging. This safety man showed up. He was 'different', and he stood there asking all sorts of questions while a crew of ironworkers moved the transformer along the rails. The ironworkers were using comealongs, and the transformer was moving so easily we did away with the dynamometer. The ironworkers were working the comelongs rapidly. The safety man wanted them to switch guys often and to have the guy on the comealongs switch hands frequently. The safety man's concern (now that the matter of stuff pulling out of the concrete was behind us) was that the ironworkers would sustain a 'repetitive stress injury' from working the comealongs. A buddy of mine standing nearby caught this, and piped back: 'The only repetitive stress injury they are likely to get will happen in the shower'. That sent the safety man running off to get someone in upper management to take us all to task. He got laughed out of that guy's office. - Stainless
- Join Date
- Feb 2008
- Location
- newark DE USA
- Posts
- 1,171
- Post Thanks / Like
- Likes (Given)
- 1
- Likes (Received)
- 106
When moving a machine a short distance on smooth concrete,you can use steel welding rod as rollers under the feet of the machine.Lifting it 3/32 of an inch is easier and safer than really lifting it.
- MattRobertsonAluminum
- Join Date
- Apr 2012
- Country
- UNITED STATES
- State/Province
- Missouri
- Posts
- 101
- Post Thanks / Like
- Likes (Given)
- 7
- Likes (Received)
- 54
We use steel rods and heavy pipes to move a lot of machines in our shop on the concrete as well. sometimes we use an engine lift as seen in the picture below. They are really useful for taking a table or head off too. Plus, they fold up out of the way.
But sometimes when we really want to move something outside we use our collapsible military helicopter crane here:
-Matt
Ozarkwoodworker.com - Cast Iron
- Join Date
- Sep 2011
- Location
- Nashville, TN
- Posts
- 443
- Post Thanks / Like
- Likes (Given)
- 57
- Likes (Received)
- 55
My mill stays in the dolly full time. I will be building one for the SBL soon. It works pretty good, I can move my Machines by my self.
- Aluminum
- Join Date
- Jun 2011
- Location
- California USa
- Posts
- 99
- Post Thanks / Like
- Likes (Given)
- 0
- Likes (Received)
- 15
For my Bridgeport I built a hydraulically actuated mobile base.
A few pumps on the hand pump and the wheels extend raising the mill about 1.5' up on the wheels. The base has two fixed side wheels and a rear castering wheel for positioning.
The build thread is over on *******: http://www.*******.com/forums/bridge..._j-head-2.html
Why can't I post computer numberic control zone string, what is that about?
Craig - Stainless
- Join Date
- Apr 2005
- Location
- Bay Area, Ca
- Posts
- 1,405
- Post Thanks / Like
- Likes (Given)
- 11
- Likes (Received)
- 183
I use a 15 ton bridge crane. The big hook has done up to 40000 lbs, and the small hook is 2-tons. Great for machinery disassembly, etc.
- Hot Rolled
- Join Date
- May 2011
- Location
- Sandy Hook, MB Canada
- Posts
- 891
- Post Thanks / Like
- Likes (Given)
- 1
- Likes (Received)
- 178
Hello Wb2vsj
These look interesting.
Hilman Rollers - Leading manufacturer of rollers, load skates, and material handling equipment - Aluminum
- Join Date
- Jan 2012
- Country
- UNITED STATES
- State/Province
- Pennsylvania
- Posts
- 75
- Post Thanks / Like
- Likes (Given)
- 300
- Likes (Received)
- 17
why didn't I think of that?????? use glass beads,Don't have far to fall
You can move massive weight using them,and you won't use much energy doin it,and when it falls it don't have far to go to hit the floor I moved a norton Surface Grinder est 1400 lb by pushing it.gust keep em under the machine and not your feet,a smooth floor helps too,try my Idea and see if it works,???Originally Posted by CiszewskiHello Wb2vsj
These look interesting.
Hilman Rollers - Leading manufacturer of rollers, load skates, and material handling equipment
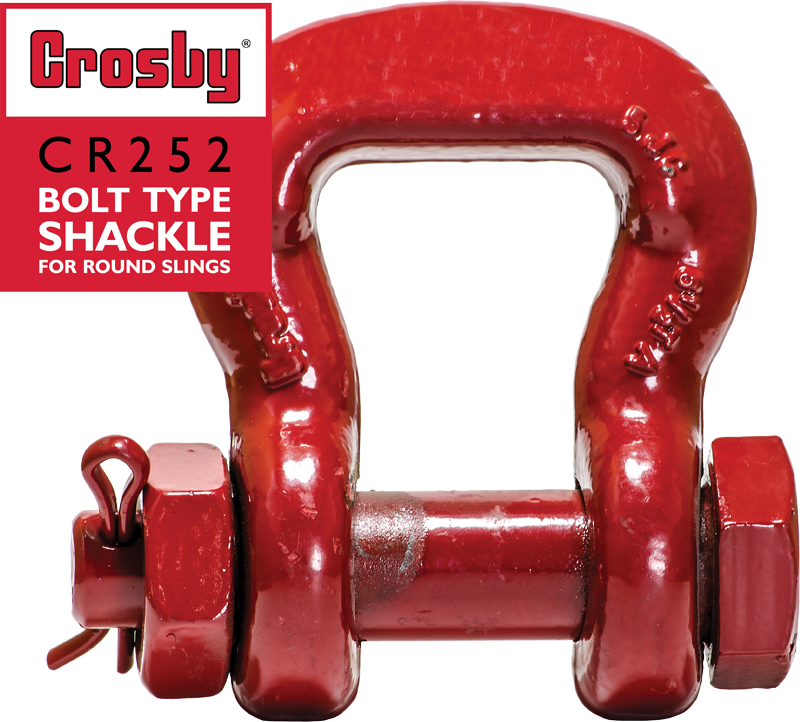
- Site Areas
- Forums
- Manufacturing Today
- Specific Machine Forums
- Open Discussion
- Commerce
- Machinery Manual, Brochure and Photo Archives
- Forum features

Bookmarks
Pad Eye Design Calculation
Posting Permissions
Pad Eye Hardware
- You may not post new threads
- You may not post replies
- You may not post attachments
- You may not edit your posts
Heavy Duty Pad Eye
- BB code is On
- Smilies are On
- [IMG] code is On
- [VIDEO] code is On
- HTML code is Off